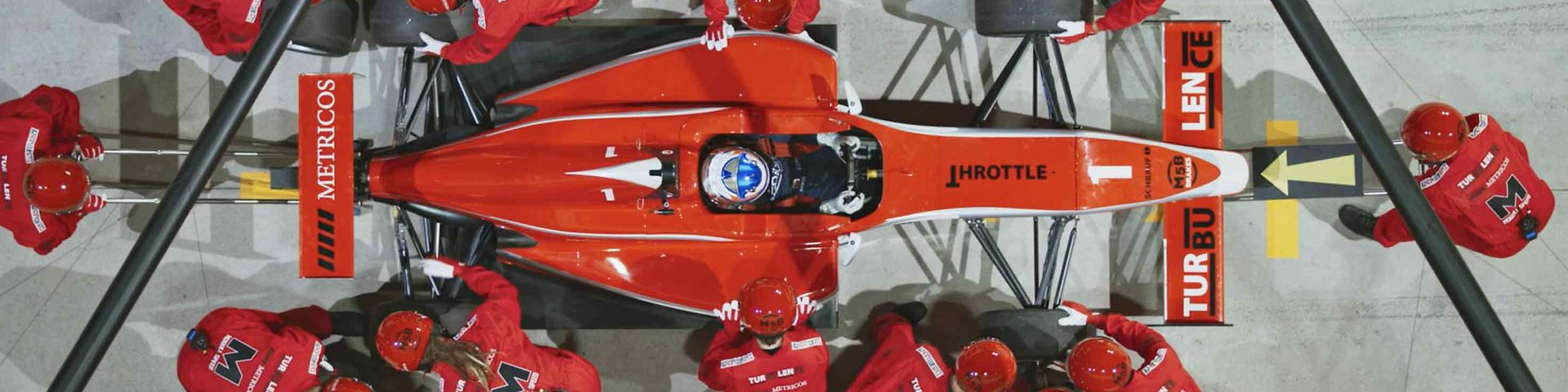
Seek and ye shall find: Tracking down spare parts with AI
DB Cargo and Partium are bringing maintenance into the 21st century.
With more than 2,700 locomotives and over 82,000 freight wagons, DB Cargo's fleet is the largest in Europe. This means Europe's biggest freight operating company has the right solution for every transport. At the same time, this size presents enormous challenges for DB Cargo's maintenance depots every day. The fleet is so complex and varied that precise documentation of the vehicles is challenging.
What has searching for spare parts been like until now?
Finding spare parts is not exactly a breeze for the technicians. Experienced staff are often very quick to find the parts they need, but sometimes even they need 10-20 minutes or more per part and per search. That might not sound like much at first, but the repercussions for vehicle maintenance are profound. After all, in train maintenance, time is the crucial factor in getting wagons and locomotives quickly back into service.
Why does finding the right part take so much time?
There are a variety of reasons: Often, the environment takes its toll on parts, leaving them worn, soiled and deformed, which complicates searches. In such cases, even our seasoned colleagues are hard pressed to identify with certainty the parts they need. And while they often know what part they are dealing with, they might not know the exact material ID needed to fetch it from storage.
What will parts searches look like in future?
With an eye to optimising and accelerating these manual processes, DB Cargo has introduced Partium, initially for 50 locomotives and freight wagons. Partium is a leading solution for recognition of spare parts and components that is now being used to help DB Cargo turn on the speed when spare parts are sought. The system taps into a broad range of information to run searches – a crucial advantage, given DB's diverse vehicle fleet and the stark differences in the extent and quality of documentation for individual locomotives and freight wagons. Partium therefore leverages nearly all DB Cargo's available information for searches, including materials management lists, material descriptions, substitutes, attributes, SAP numbers, warehouse inventories, storage locations, rolling stock classes, manufacturers, item numbers and other information.
Going forward, this is what searching for the spare parts with Partium will look like:
Staff use the system with a mobile app installed on their tablets. The technicians:
- start looking for the part on the locomotive or freight wagon
- reliably identify the right part locally through a visual image search, semantic text search and other search functions
- access the storage location directly in the mobile app
- in future, display current inventory directly in the app
- contact the material warehouse and request the retrieval of the part in question from storage
In practice, this considerably expedites the search for materials. The technicians are spared the need to walk for 5-10 minutes to pore through document stores for the relevant information. Downstream processes, such as retrieval of materials from storage, are faster and more reliable. The new system frees up team leaders from the need to help with searches, too. Instead they can quickly prepare the papers needed to retrieve parts from storage using information from the Partium app. "This is my absolute favourite app. You can reliably find all the information about spare parts, and the information about storage locations is particularly invaluable. This used to require SAP access, which hardly anyone at the depot has," says Julian Drescher, project manager for smart material recognition (iMate) at DB Cargo.
Partium currently contains some 9,000 parts in their entirety. The system has been rolled out at six maintenance plants with 35-100 technicians working in maintenance. A speedy rollout to all DB Cargo's 11 depots and 15 satellite depots is in the works.
Contact our expert now.
Julian Drescher
Project manager intelligent material recognition (iMate) DB Cargo